さようなら、可動部のガタつき。
Expander エクスパンダー
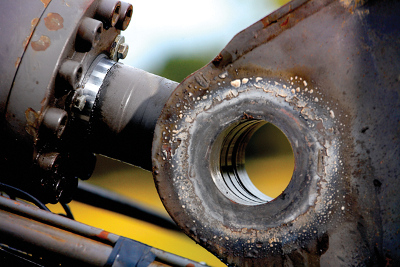
ピン穴の摩耗がもたらすマシンの品質への影響
従来のピンでは、ピン穴とピンの間に僅かな隙間が生じます。ピンの軸はその隙間のためにピン穴内部で動き、マシンの稼働にガタつきを生じさせるだけでなく、軸が繰り返し衝突することで衝突部が摩耗し、楕円状に変形してしまう事象が当たり前になっています。
一旦ピン穴に摩耗が発生すると、修繕工程では肉盛りや表面調整など大変な労力と時間、なによりコストを要する作業が必要です。これらは全てマシンを購入したお客様にとっては維持費の負担となり、上記のような修繕も無限に行えるものではないため、マシン自体の寿命にも大きく影響しています。
あらゆる設備機器の可動部を摩耗から守るソリューション
エクスパンダー・システムは、その可動部に起こる摩耗をピン穴内部の遊び(隙間)をゼロにする独自機構によって解決し、ガタつきや額な肉盛補修、頻繁なブッシュ交換を撲滅します。建設・土木・林業で使用される重機や工場設備にとって、可動部の摩耗解決は維持費削減に理想的なソリューションとなります。
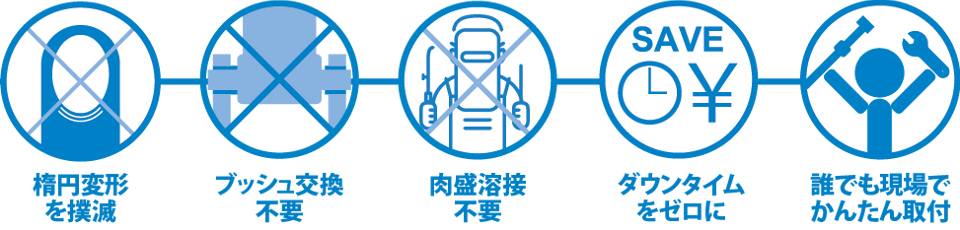
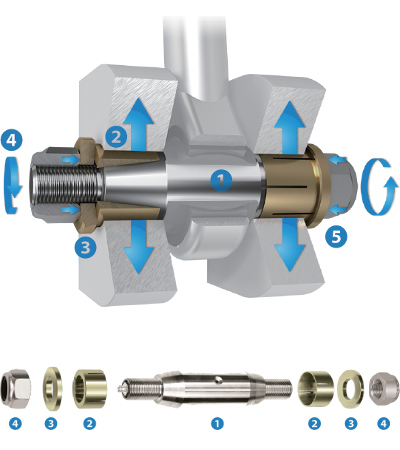
エクスパンダー・システムの仕組み
- 1. テーパー付ピン
- 既存のピン穴に、穴加工なしでそのまま挿し入れます。
- 2. 拡張スリーブ
- 次に、スリットが入った拡張スリーブを取り付けます。
- 3. テンションワッシャー
- 後にスリーブを内側に押し込んで拡張させるテンションワッシャーを取り付けます。
- 4. ナットまたはボルト
- 最後に両端のナット(またはボルト)を締め込むことで、テンションワッシャーが拡張スリーブを内側に押し込んで行きます。拡張スリーブはピンのテーパーに沿ってスリットが開いて拡張し、ピン穴との隙間を埋めてしまいます。
- 5. 取外し作業
- 取り外しはこの逆で、ナット(またはボルト)を緩めて順番に取り外しを行います。特殊な工具や切断の必要はありません。
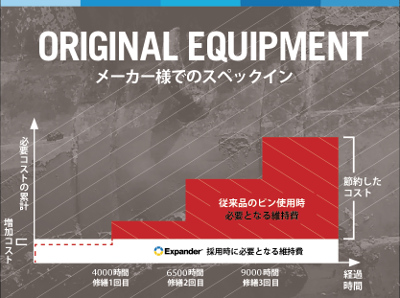
エクスパンダー・システム導入のメリット
– メーカー様でのスペックインの場合 –
- ピン穴摩耗解消によるマシン品質(寿命)向上
- 本製品を純正品として貴社からの販売が可能
- 3D CADEXによる迅速な設計対応と正確な性能評価
- 標準品なら最短48営業時間以内に出荷が可能
- カスタム品も設計開始から1ヶ月程度で納入可能
- 設計者様・サービス担当者様へのトレーニング
- 10年間または10,000時間の機能保証付
- 販売先からの修繕依頼対応の低減
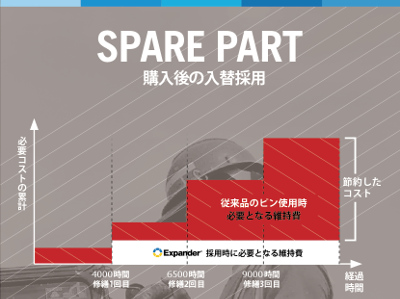
エクスパンダー・システム導入のメリット
– 購入後の入替採用の場合 –
- ピン穴の修繕、取付時の穴加工・肉盛が不要
- 上記にて修繕費・修繕期間を大幅に削減
- 簡単・迅速な取付/取外し作業で、誰でも作業可能
- 標準品なら最短48営業時間以内に出荷が可能
- カスタム品も設計開始から1ヶ月程度で納入可能
- 設計者様・サービス担当者様へのトレーニング
- 古い型式のマシンでもマシン寿命の延命が可能
- 10年間または10,000時間の機能保証付
エクスパンダー・システムと従来ピンとの取付作業比較
BEFORE: 従来のピンを使用する際の取付作業(修繕時)
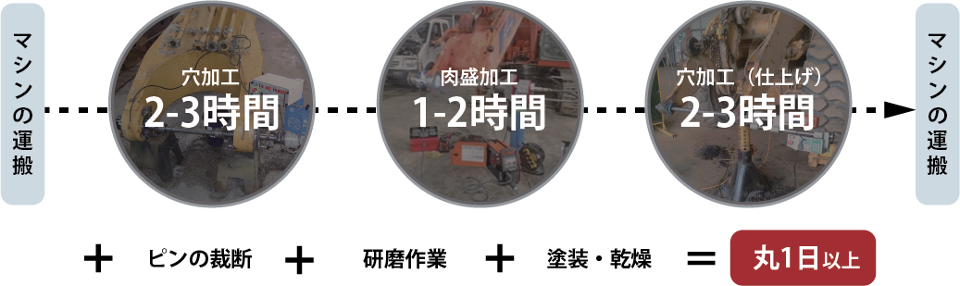
従来品のピンを使用していた場合では、まず現場作業ではリペアができないため、サービスセンターまでマシンを運搬するところからスタートします。しかし、サービスセンターからも即時引取に来るわけではなく、この時点で数時間~1日以上のロスが発生します。各作業工程に要する時間だけでも従来品のピンは、取り外しの際にピンをカットする必要があったり、研磨、塗装・乾燥が発生するため丸1日以上を要し、作業完了後もすぐに手元に運搬されて来るとは限りません。結局のところ、丸1日でマシンが修繕されて手元に帰ってくることは殆ど無いのが現状です。
AFTER: エクスパンダー・システムを使用する際の取付作業
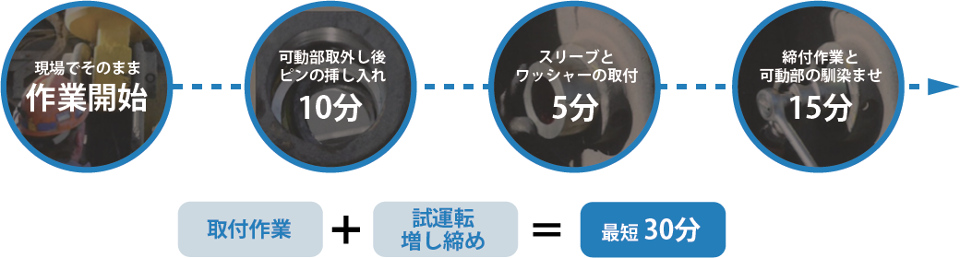
エクスパンダー・システムの取付作業では、ピン穴の摩耗具合が余程酷くない限りは、そのままテーパー付のピンを挿し入れるところから作業を開始できます。そのため、エクスパンダーは現場で取付/取外しが可能で、現場作業が可能というだけで、丸1日以上の時間を節約できる可能性があります。また、取付もページ上部の解説のある通り、ピンを挿し入れた後に両側にスリーブ、ワッシャーの順に取り付けた後、ナット(またはボルト)を締め込むだけです。実際には可動部を馴染ませるために可動域いっぱいまで何度かマシンを動かした後に最終的に増し締めを行いますが、その時間を考慮しても、最短で30分あれば交換作業が可能となります。
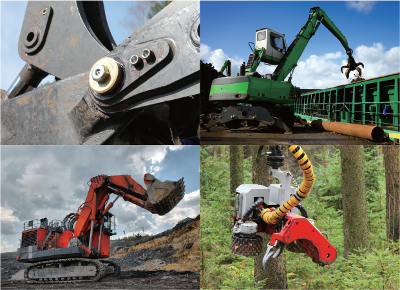
パワーショベル、バックホー等
アーム可動式建設機械での使用
どの可動部にもオールラウンドに使用でき、摩耗量が大きなピン穴に大きな効果
エクスパンダー・システムの最大のメリットは、ピン穴の摩耗を防止することでマシン自身の寿命を延命することにあります。そのため、最も大きな応力がかかるアーム可動部の駆動軸として、そして油圧シリンダーの接続部のピンとしての採用事例が最も豊富です。もちろん、使用箇所の形状やベアリングの有無、可動部近くの障害物の有無等によってエクスパンダーの形状も様々なものをご使用いただけます。
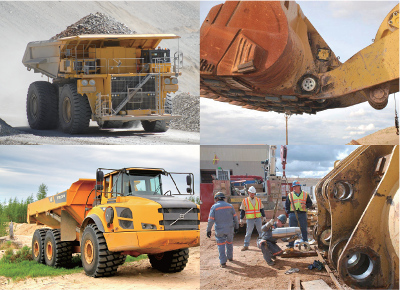
ホイールローダーやブルドーザー等
車両型重機での使用
荷台やステアリングのシリンダー接続部、ブルドーザーのアタッチメントにも
エクスパンダー・システムは、ピン穴の隙間をゼロにすることができます。これは、マシン可動部のガタつきを最小限に抑えられることを意味しており、運搬車両に限らず、あらゆる可動部の動きを安定させます。想像を絶する大きな荷重を、比較的長時間に渡って支え続ける運搬車両ではこのようなガタつきの低減に加え、現場の安全性向上にも貢献いたします。ステアリングシリンダーにおいては、スウェーデンの大手建機メーカー様にて50,000時間(ほぼ6年間)連続での実地耐久試験を耐え抜き、試験後のエクスパンダーは新品時とほぼ変わらない機能を残していました。
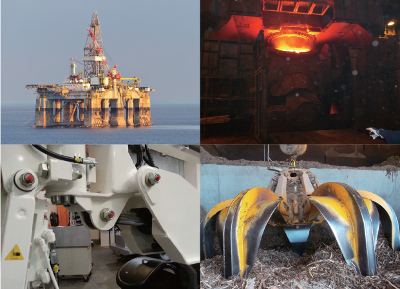
製鉄所、洋上施設や生産プラント設備にも
洋上施設クレーンや製鉄所の圧延設備、空港・港湾設備やごみ焼却場等あらゆる可動部に
エクスパンダー・システムは、用途ごとに細分化された従来のピンとは違い、あらゆる設備機器の可動部に使用できるオールラウンドな製品です。過去に最も多いのはやはり建機での採用事例ですが、洋上施設や建設用クレーン、各種向上内での吊り下げ式クレーン、製鉄所や各種生産プラント、ごみ処理施設等、幅広い産業の設備機器で採用されています。
可動部にピンを使用し、そしてピン穴の摩耗が課題となっている全ての設備機器において、エクスパンダー・システムは革命的なソリューションになり得ます。
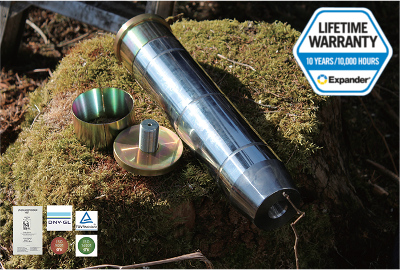
エクスパンダー・システムが取得した主な証明書・許認可
- アルフレッド・ノーベル財団開発賞受賞
- 品質マネジメントISO9001:2000および環境マネジメントISO14001認証取得
- TÜV Rheinland認可証取得
- DNVによる認可証取得
- 欧州主要企画であるDNV2.22、DNV-OS-E101および米国主要企画API specification 8C取得
- 製品設計時の計算方式にてDNV認可を取得
- ピン材料にてDIN(ドイツ工業規格)、EN(欧州統一規格)、ISO、ASTM(米国試験材料協会)、AISI(米国鉄鋼協会)、ANSI(米国国家規格協会)認可取得
- ボルボ建機社の実地耐久試験にて連続50,000時間稼働
EXPANDER SYSTEM FAQ – よくある質問とその回答集
Q. エクスパンダーの納期はどれくらいかかるの?
標準品の場合、48時間後に出荷し輸送を含めて約2週間以内です(基本的には空輸)。
Q. エクスパンダーの材質は?
ピンはSCM435。高強度ステンレスもあり。 ボルト・ナット・スリーブはS45C相当。SUS製もあります。
Q. ピン径の寸法公差は?
標準で「h7」、大径になると「f7」の可能性もあります。その他の公差オプションもありますが、価格と納期が変動します。
Q. 耐熱温度は?
標準品(鉄製)で-30℃から200℃。全てSUS製の場合は最大550℃となります。
Q. メーカー純正品じゃないから保証が効かなくなるのが怖い・・・
車両メーカーの保証は効かなくなってしまいますが、エクスパンダー自体には10年間または10,000運転時間の機能保証が付与されています。
Q. 特殊な工具が必要では?
トルクレンチ、ハンマー等の一般工具があれば大丈夫です。
Q. どうやって取り外すの?
どなたでも簡単に現場で行えます。わかりやすいご説明資料を製品に同梱しています。
Q. 最小径と最大径は?
製品タイプにもよりますが、概ねφ10mm~φ400mm程度まで対応可能です。上記範囲外のサイズでも、スペシャル品として対応可能です。
Q. 車両のモデルがかなり古い型式で使い込まれているが使える?
型式の古さに関わりなくご使用いただけます。現状で安全に稼働できる車両であればエクスパンダーを使用して、これ以上の補修作業を無くして寿命を延ばすことができる点も本製品のメリットです。